Folien Beschichtung / Lohnbeschichtung
Kundenspezifische Beschichtung auf Folien und Geweben - Entwicklung und Auftragsfertigung
Seit über 60 Jahren werden bei CMC Klebetechnik Folien im Rolle-zu-Rolle Verfahren beschichtet. Schon immer haben wir aufmerksam zugehört, was unsere Kunden tatsächlich benötigen. Dieses Wissen und diese Erfahrung nutzen wir heute, um auch in Sachen Lohnbeschichtungen Ihr kompetenter Partner zu sein.
Auf zwei modernen Beschichtungsanlagen bringen wir mit Geschwindigkeiten von 4 m/min bis 50 m/min auf bis zu 1.900mm Breite Funktionalisierungen auf Folien und Gewebe auf. Die Beschichtungsanlagen werden ergänzt durch etliche Schneid- und Stanzanlagen. Für hochwertige Beschichtungen und bei hohen Auftragsmengen nutzt man eher die minimal möglichen Geschwindigkeiten. Für unproblematischere Produkte und geringe Auftragsmengen hingegen kann man mit höheren Geschwindigkeiten beschichten. Diese hohe Flexibilität ermöglicht es CMC, kleine und große Projekte wirtschaftlich handhaben zu können. Außerdem ist der Einrichtaufwand und Einfahrverlust dadurch gering.
Folienbeschichtungen werden jedoch nicht nur für eigene Produkte durchgeführt, sondern beschichtete Folien werden auch im Lohn gefertigt (Lohnfertigung). Dabei kann der Kunde entweder die Folie, die Beschichtungsmasse oder beides beistellen. Die Anlagentechnik inklusiv des Bedienpersonal kann für Beschichtungsversuche auch stundenweise gemietet werden.
Üblicherweise ergibt sich ein dreitstufiger Entwicklungsprozess für Auftragsbeschichtungen (Lohnausrüstungen): In der (1) Entwicklungsphase geht es von ersten DIN A4 Mustern nach Bedarf auf unseren (2) Labor-Coater. Hier kann man die späteren Beschichtungsparameter ermitteln oder Produktoptimierungen durchführen. Danach werden dann bei Erfolg erste (3) Musterproduktionen auf den Großbeschichtungsanlagen gefertigt. Nach einer Erprobungsphase von drei gleichartig erfolgten Beschichtungen beginnt in der Regel die Serienlieferung.
CMC Klebetechnik bietet
- Beschichtungen auf flexiblen Endlosmaterialien
- Beschichtungen für Hostaphan® - Polyesterfolien
- Beschichtungen für Kapton® - Poylimidfolien
- Beschichtungen für Mylar® - Polyesterfolien
- Beschichtungen für Nomex® - Aramamidpapier
- Beschichtungen für Teflon® - PTFE-Folien
- Beschichtungen für Victrex® - PEEK-Folien
- Beschichtungen für Torelina® - PPS-Folien
- Beschichtungen von ETFE-Folien
- Beschichtungen von Glasgeweben und Vliesen
- Funktionalisieren von Folien
- Papierbeschichtungen
- Beschichtungen für Teonex® - PEN-Folien
- Beschichtungen für PVC - Folien
- Beschichtungen von Kupferfolie
- Beschichtungen von Aluminiumfolie
-
ganz allgemein Beschichtungen auf Rollenware
mit
- Acrylatklebstoffen
- Reinacrylat Klebstoffen
- Polysiloxanklebstoffen
- Silikonklebern
- Kautschuk Klebstoffen
- Heißsiegelklebern
- PU-Klebstoffen
- Polyesterharz Klebstoffen
Bei Bedarf auch andere Beschichtungsmassen wie Latex, wärmeleitende Silikone, Mehrkomponenten-Systeme, Acrylatbeschichtungen und vieles mehr.
Individuelle Beschichtungen von Folien
Von der ersten Idee an steht die CMC Klebetechnik mit ihrem Fertigungs-KnowHow, der flexiblen Anlagentechnik und dem umfassenden Material-KnowHow seinen Kunden zur Seite. Denn individuelle Klebebeschichtungen erfordern eine Menge spezifischen Wissens, damit am Ende ein erfolgreiches, neues Produkt entsteht. Ein erfahrenes Team aus Anwendungsberatern, Entwicklern und Mitarbeitern aus der Produktion begleiten die Entwicklungsabteilung des Kunden auf dem Weg zu einer optimalen Lösung.
Um Kunden möglichst effizient bei Ihrer Produktentwicklung zu unterstützen, hören die Anwendungsspezialisten von CMC Klebetechnik genau zu und übersetzen die Kundenanforderungen in die Sprache der Folienhersteller, Klebstofflieferanten und Beschichtungsführer an den Beschichtungsanlagen. Die frühzeitige Einbindung in den Entwicklungsprozess vermindert dabei auf beiden Seiten die Anzahl eventueller Fehlversuche.
Der Entwicklungsprozess kann bei der CMC Klebetechnik in vier Schritte eingeteilt werden:
Eigenschaftsprofil
In gemeinsamen Gesprächen werden die Rahmenbedingungen festgelegt, die für die Beschichtungslösung gelten sollen. Sei es, dass zum Beispiel eine wiederlösbare Klebeverbindung benötigt wird, eine spezielle Funktionalisierung oder eine Beschichtung mit thermischer Leitfähigkeit.
Materialauswahl
Mit der Erfahrung aus zahlreichen Auftragsentwicklungen entwickelt CMC Klebetechnik zusammen mit dem Kunden einen Projektplan und definiert die passende Beschichtungstechnik. Auch bei der Auswahl geeigneter Produkte oder der Modifikation bestehender Lösungen unterstützt CMC Klebetechnik den Kunden. Das Endprodukt kann oft erst durch eine Anpassung von Folien und Beschichtungsmassen an die Fertigungstechnik hergestellt werden.
Optimierung
Nach der Entwicklung einer Beschichtungslösung endet unser Service nicht. Auch nach dem Start der Serienproduktion wird in einem ständigen Optimierungsprozess weiter nach Einsparpotenzialen gesucht. Ergebnisse dieses Prozesses werden dem Kunden vorgestellt, so dass er selbst entscheiden kann, welche Veränderungen er gerne umgesetzt hätte.
Zu dem Service von CMC Klebetechnik gehört auch, dass Kunden im Rahmen der Möglichkeiten bei der Produktionsplanung unterstützt werden. Das betrifft vor allem das Bereitstellen der Produkte in der optimalen Form. Akkurat geschnittene Klebe-Rollen, exakt gestanzte Formteile oder verarbeitungsgerecht konfektionierte Laminate helfen, eine reibungslose Fertigung zu erzielen. Außerdem können auf diese Weise Taktzeiten nahezu immer deutlich reduziert werden und damit die Stückkosten.
Doch auch perfekte Lieferzeiten, eine abgestimmte Lagerhaltung, Sicherheitsbestände und die rechtzeitige Beschaffung von Rohstoffen gehören zum Service und optimieren im Laufe der Zeit die Zusammenarbeit.
Langfristige Partnerschaft
Seit über 60 Jahren beschichtet die CMC Klebetechnik, Frankenthal, Folien mit Klebstoffen und anderen Beschichtungen. Viele Firmen sind bereits Jahrzehnte Kunden und vertrauen auf die Flexibilität und Stabilität des Unternehmens. Dieses Vertrauen muss man sich erarbeiten – darum ist auch bei kundenspezifischen Beschichtungen eine perfekte Supply Chain mit einer zuverlässigen Rückverfolgbarkeit selbstverständlich. Denn nur langfristige Partnerschaften lassen eine vertrauenswürdige, wertschöpfende Zusammenarbeit entstehen.
Kundenspezifische Lösungen
CMC Klebetechnik ist ein leistungsfähiger, kompetenter Entwicklungspartner bei Konzeption und Umsetzung von kundenspezifischen Beschichtungslösungen auf Folien, Geweben und Vliesen. Wir verstehen Ihre Anforderung und übersetzen sie professionell in Produkte und Verfahren.
Das bedeutet für Sie, professionelle Folienbeschichtungen aus einer Hand. Obwohl es auf dem Markt eine sehr große Menge unterschiedlichster Kombinationen aus Folie, Gewebe oder Papier mit (Kleber-) Beschichtungen gibt, kann eine individuelle Lohnbeschichtung von Folien wesentlich dazu beitragen, ein Produkt marktfähig zu machen oder überhaupt herstellen zu können. Eine optimale Anpassung einer beschichteten Folie an die von Ihren eingesetzte Technik der Weiterverarbeitung führt zu einer Kostenreduktion und damit zu einem mitentscheidenden Wettbewerbsvorteil für Ihr Unternehmen.
Beschichtungen von Folien, ob nun als Lohnbeschichtung von Folien oder aber als kundenspezifisch entwickelte Folienbeschichtung bieten hervorragende Lösungsmöglichkeiten an.
Kompetente Beratung
Sie erhalten von uns Hilfe bei der Entwicklung von Beschichtungsrezepturen, bei der Auswahl geeigneter Produkte (Folien, Kleber, etc.) und dem Beschichtungsverfahren. Dafür stehen ein eigenes Entwicklungslabor, ein erfahrener Mitarbeiterstamm, gute Beziehungen zu international tätigen Lieferanten und zwei moderne, flexible Beschichtungsanlagen bis 1.900 mm Breite zur Verfügung. Es können Lösemittel - und Dispersionsbeschichtungen durchgeführt werden.
Weitergehende Verfahrensschritte wie Laminieren und Kaschieren sowie Schneiden und Stanzen komplettieren unser Leistungsangebot.
Durch die Möglichkeit der Verwendung von Lösemittel- und Dispersionsklebern und den flexiblen, rüstkostenarmen Beschichtungsanlagen ergeben sich weitergehendere Möglichkeiten als bei einem spezialisierten Beschichter.
Hier finden Sie unsere Rahmenbedingungen für Lohnbeschichtungen.
Hinweis zur Grobkalkulation: Es gibt im Beschichtungsprozess mehrere Faktoren, die dazu beitragen, dass nicht 100% der eingesetzten Materialien auch am Ende im fertig beschichteten Produkt auftauchen. Dies sind z.B. Einfahrverluste, ein technisch bedingter beschichtungsfreier Rand (fällt bei schmalen Ausgangsbreiten stärker ins Gewicht), Reste an Beschichtungsmasse in den Behältern, Teilungsverluste beim Schneiden in Schmalbreiten usw.
Ohne dies als generelle Regel ansetzen zu können, sollten Verluste von ca. 5-15% in die Kostenkalkulation eingerechnet werden.
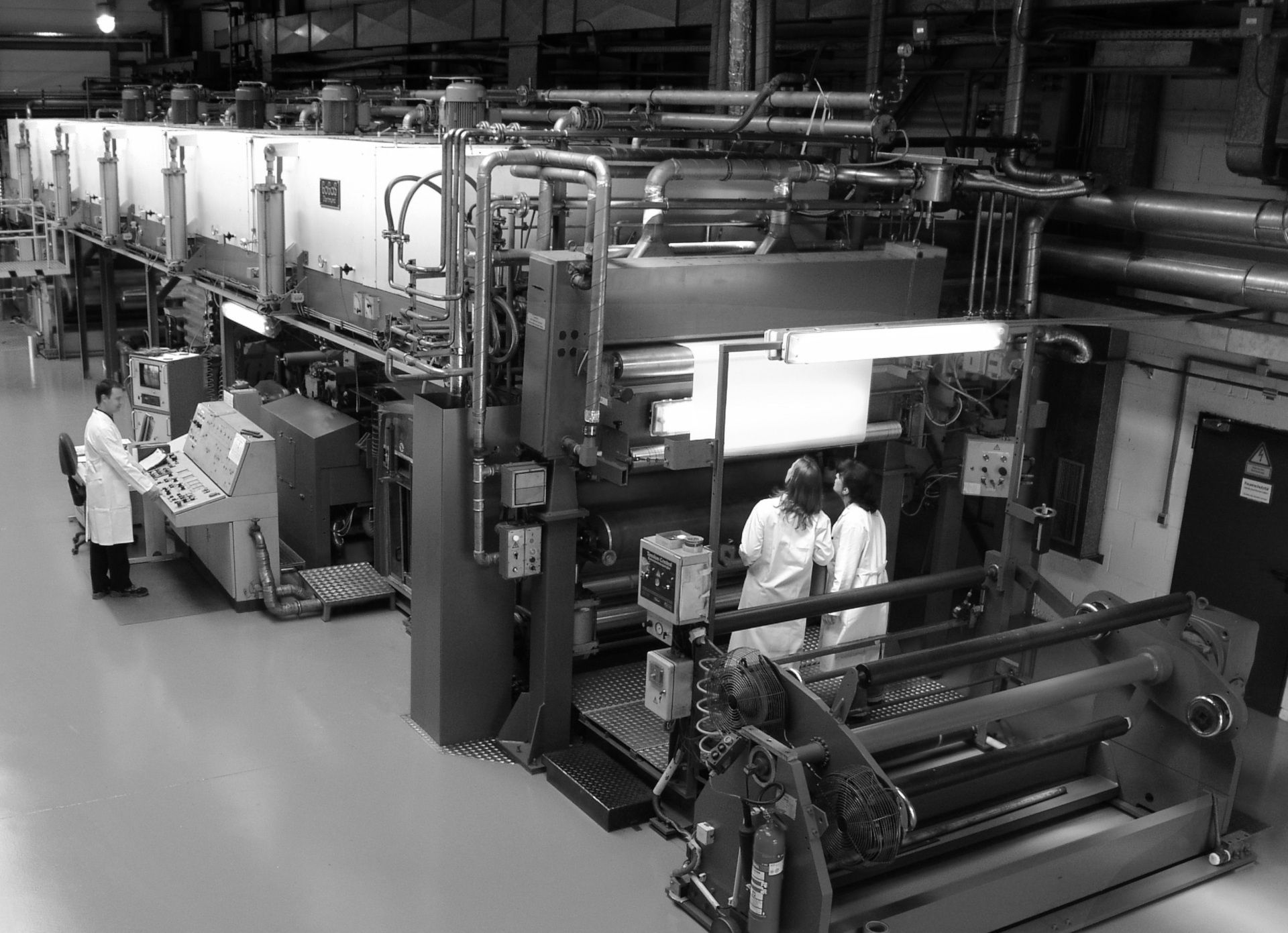
Warum Kunden Produktionen verlagern
- Sie haben nicht die erforderlichen Entwicklungskapazitäten
- Es kommt zu Engpässen in der eigenen Produktion
- Sie haben nicht die erforderlichen Anlagen
- Sie möchten sich lieber auf Ihre Kernkompetenzen konzentrieren
Sogar andere Beschichter nutzen die Möglichkeiten, weil häufig keine Konkurrenzsituation vorliegt (andere Kunden, andere Märkte, andere Technik).
Interessierten Kunden bieten wir mit unseren verschiedenen Beschichtungsanlagen und der jahrzehntelangen Erfahrung umfangreiche Möglichkeiten, kundeneigene Lösungen zu realisieren. Dabei ist es egal, ob Sie eine neue Folie mit einer Standardbeschichtung versehen oder eine neue Beschichtungsmasse auf eine beigestellte Folie aufbringen lassen wollen. Sie erhalten Unterstützung bei der Formulierung der Beschichtungsmasse durch unsere Entwicklungsabteilung (unsere Möglichkeiten sind nicht nur auf einen "Kleber"-Auftrag beschränkt).
Vor der Fertigung auf den Produktionsanlagen können auf einer Pilot-Beschichtungsanlage die ersten Entwicklungsschritte durchgeführt werden, um so bereits optimierte Bedingungen für die erste Versuchsbeschichtung zu erhalten.
Unsere Leistungen
- Mehrere flexible Beschichtungsanlagen
- Vielzahl an Standardprodukten
- Eine eigene Entwicklungsabteilung
- Fundierte Fachberatung und Projektbegleitung
- Kundenspezifische Entwicklung und Fertigung
- Qualitätsfertigung in Deutschland
- Individualität der Betreuung, Flexibilität
- Kundenorientiertes Arbeiten (zum Nutzen des Kunden)
- Flexibel bei der Gestaltung der Produktaufmachung (Länge, Breite, VE?)
- Stimmigkeit von Preis und Leistung
- Verlässliche Qualität
- Partner für Großindustrie und Mittelstand (für alle Losgrößen offen)
- Zusammenarbeit mit namhaften Lieferanten aus der internationalen Großchemie
- Erfahrung in Material und Anwendung
- Fachberatung (auch vor Ort, kein reiner Katalogverkauf)
- IMDS, RoHS, UL, IEC, ISO 9001, ISO 14001
Beschichtungstechniken
Es stehen zwei Beschichtungsanlagen für wasserbasierende und lösemittelbasierende Beschichtungen zur Verfügung. Darauf können Auftragsgewichte zwischen ca. 6 gr/m² bis 2000 gr/m² beschichtet werden - und das auf bis zu 1.900 mm Breite. Üblicherweise ergibt sich ein dreitstufiger Entwicklungsprozess für Auftragsbeschichtungen (Lohnausrüstungen): In der Entwicklungsphase geht es von ersten DIN A4 Mustern nach Bedarf auf unseren Labor-Coater. Hier kann man die späteren Beschichtungsparameter ermitteln oder Produktoptimierungen durchführen. Danach werden dann bei Erfolg erste Musterproduktionen auf den Großbeschichtungsanlagen gefertigt. Unsere erfahrenen Mitarbeiter begleiten Sie - vom ersten Beratungsgespräch bis zu Serienfertigung. Seien Sie dabei, wenn Ihr eigenes Produkt entsteht: Sie sind herzlich eingeladen zu einem Besuch.
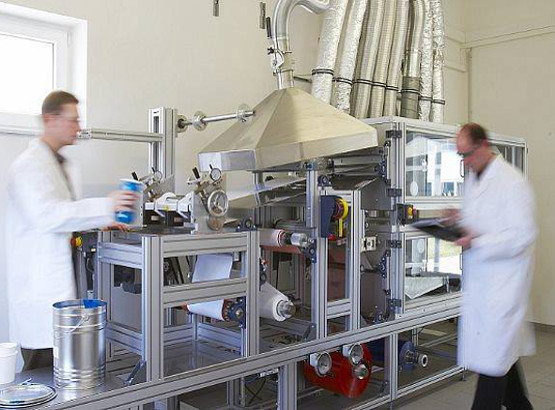
Pilotcoater (Laborkanal)
Beschichtungen auf dem Pilotcoater bieten die Möglichkeit, produktionsnah größere Mustermengen zu fertigen. Die Parameter können am Pilotcoater schneller geändert und so unterschiedliche Einstellungen getestet werden. Dadurch reduziert sich deutlich die Gefahr einer Fehlentwicklung bei verhältnismäßig geringen Kosten.
Für Beistellungen gilt als Maximalmaße eine Breite von 300mm und ca. 250mm Rollenaußendurchmesser
Die Anlage wird von dem gut ausgebildeten Laborpersonal bedient und der Versuch komplett begleitet sowie die Ergebnisse intern dokumentiert, um reproduzierbar erneute Versuche durchführen zu können.
Die hierfür anfallenden Kosten trägt der Auftraggeber gemäß Angebot. Dies gilt auch bei einem Misserfolg.
Hauptbeschichtungsanlage
Es können lösemittel- und wasserbasierende Systeme verarbeitet werden. Die maximale Breite beträgt 1,50 m und 1,90 m.
Auf den Hauptbeschichtungsanlagen werden die tatsächlich notwendigen Parameter für eine Serienbeschichtung ermittelt. Erst mit diesen Daten ist eine endgültige Kalkulation des Beschichtungspreises möglich.
Die erste(n) Versuchsbeschichtung auf den Hauptanlagen kann einen erhöhten Abfallanteil erfordern, bis die richtigen Parameter gefunden sind. In ganz seltenen Fällen kann ein Abbruch notwendig sein. Die angefallenen Kosten müssen dennoch berechnet werden.
Kennzahlen der Beschichtungsanlagen:
- Auftragsstärke: je nach Beschichtungsanlage ca. 8 µm - 60 µm, bei 100% Systemen bis 2.000 µm
- Auftragsart: Rollrakel, Kommarakel, auch streifenförmige Beschichtungen möglich
- Breite: je nach Anlage mind. ca. 500 mm bis max. 1900 mm
- Trägerstärke: abhängig vom Material ab ca. 6 µm bis ca. 1 mm
- Art der Beschichtungsmasse: Lösemittel-basierend, Dispersion, 100%-System, 2K-System
- Trocknungsart: Heißluft unter Atmosphäre
- Maximale Temperatur: bis 155°C (auch zur Vernetzung)
- Oberflächenaktivierung: Coronavorbehandlung
Weitere Möglichkeiten: Auftrennen in mehrere Rollen, Laminieren, Abdecken mit silikonisierten Folien/ Papieren
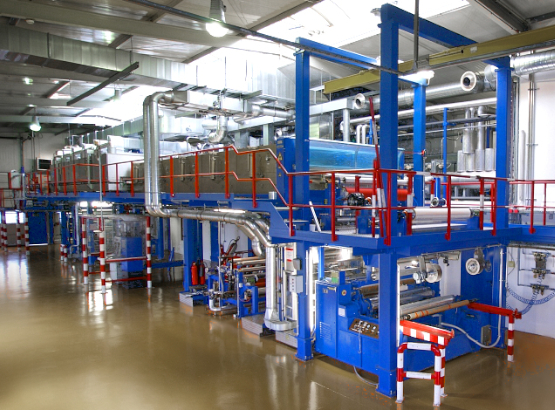
Die wesentlichen Kosten bestimmenden Parameter einer Beschichtung sind:
- Breite der zu beschichtenden Ware
- Menge (kleine Menge, großer Rüstaufwand)
- Geschwindigkeit, mit der aufgetragen werden kann (Auftragsmenge, Lösemittel)
- Anzahl der Beschichtungsdurchgänge (doppelseitig = 2 Beschichtungsdurchgänge)
- Art von Träger und Beschichtungsmasse, sofern nicht beigestellt
Wir nehmen unsere Verantwortung für die Umwelt ernst: Alle unsere Lösemittel werden durch thermische Oxydation (RNV) abgebaut. Unsere Anlagen sind technisch darauf ausgelegt, in einem weiten Massenauftragsbereich arbeiten zu können und mit einer großen Vielfalt an Trägermaterialien und Lösemittelsystemen zurecht zu kommen. Unsere systematische Vorgehensweise sichert bei der Entwicklung und Fertigung eine professionelle, flexible und zielorientierte Arbeit - zu Ihrem Nutzen.
Lohnbeschichtungen
Welches Produkt hat am ehesten die Chance, bei einer gegebenen Anwendung eingesetzt zu werden?
Darauf gibt es zwei Antworten: in vielen Fällen entscheidet der Preis. Doch oft sind auch die technischen Argumente für oder gegen den Einsatz ausschlaggebend.
In den meisten Projekten ist ein maßgeschneidertes Produkt die beste Lösung, da es dem Kunden ein Maximum an Funktionalität bietet. Oft spielt dann der geringfügig höhere Preis keine Rolle.
Folien, Gewebe oder Papiere sind alles bahnförmige Produkte, die bei der CMC Klebetechnik GmbH veredelt werden können. Seien es rutschfeste Oberflächen, klebstarke Haftbeschichtungen, spannungsfeste Isolationen, temperaturbeständige Trägerwerkstoffe, elektromagnetische Abschirmungen, die Reihe an Beispielen ließe sich endlos weiter ausdehnen.
Allen Anwendungen gemeinsam ist die hohe Anpassung der veredelten Bahnware an die Erfordernisse der Anwendung.
In den meisten Fällen sind die Bedarfsmengen für solche spezialisierten Lösungen relativ gering und können nicht von Massenfertigern hergestellt werden. Denn deren Anlagen sind darauf spezialisiert, große Mengen einer möglichst immer gleichen Produktgruppe möglichst kostengünstig zu fertigen. Schon das Anfahren solcher Großanlagen verschlingt eine Unmenge an Rohmaterial, ohne das bereits ein Quadratmeter Nutzware gefertigt wäre.
Die Anlagentechnik der CMC Klebetechnik ist extrem flexibel. Beschichtungsgeschwindigkeiten zwischen 0,5 m/min bis 50 m/min erlauben hochpräzise oder kostengünstige Beschichtungen. Integrierte Coronaanlagen verbessern die Benetzbarkeit der Folien und die Haftung der Beschichtungen. Eine laufende In-Line Überwachung sowie Qualitätsprüfungen an jeder produzierten Rolle im hauseigenen Labor gewährleisten ein gleichbleibendes Qualitätsniveau.
Durch die flexible Anlagentechnik können kleinere Aufträge ab 500 qm genauso gefertigt werden wie Großfertigungen mit einigen Hunderttausend Quadratmeter pro Jahr.
Es kann zwischen Dispersions- und Lösemittelbeschichtungen gewählt werden. Auch die Auftragstechnologie an sich ist flexibel gehalten, so dass ein extrem weiter Dickenbereich von ca. 10µm bis ca. 1000µm beschichtet werden kann.
Ein erfahrenes Team von Spezialisten unterstützt den Kunden dabei, die richtige Kombination von Träger und Beschichtung zu finden. Ausgezeichnete Verbindungen zu vielen Herstellern von Bahnware und Beschichtungsmassen helfen dabei dem Entwicklerteam, aus einer großen Anzahl von Ausgangsstoffen den für die Anwendung passenden auszuwählen.
Alternativ ist es auch möglich, bereits vorhandene Lösungen auf den Anlagen im Lohn beschichten zu lassen. Die über mehrere Dekaden angesammelte Kompetenz in Sachen Beschichten steht dann dem Kunden als Dienstleistung (Lohnbeschichtung) zur Verfügung, in den meisten Fällen kann er sogar dabei sein, wenn sein Produkt auf der Anlage produziert wird.
CMC Klebetechnik bietet eine One-Stop-Lösung:
Hilfe bei der Entwicklung, der Materialauswahl und -beschaffung, Probefertigung auf einem Laborkanal und schließlich Serienfertigung. Anschließend kann die Ware geschnitten, formatiert oder gestanzt werden.
Streifenbeschichtung
Nicht immer ist ein vollflächiger Klebstoffauftrag vorteilhaft. Werden dünne Folien mit solchen Klebebändern gespeisst, kann auspressender Klebstoff die Lagen miteinander verkleben. Oder Stanzteile aus solchen Klebefolien lassen sich nur schwer vom Träger lösen, weil es keine leicht greifbare Anfasslasche gibt.
CMC Klebetechnik bietet für diese und andere Aufgabenstellung streifenbeschichtete Folien an. Diese Klebefolien erhalten dazu in beliebigen Abständen und Breiten einen streifenförmigen Klebstoffauftrag.
Technisch gesehen wird dabei in dem Beschichtungswerk eine Maske eingelegt, die den zunächst flüssigen Klebstoff nur auf die gewünschten Bereiche der Folie aufträgt. Diese Maske kann individuell nach Kundenwünschen gestaltet werden.
Beispiele für die kundenspezifischen Möglichkeiten sehen Sie hier in der Zeichnung (rechts).
Natürlich können auch einzelne Rollen mit Streifenbeschichtung angeboten werden. Daraus können zum Beispiel Stanzteile mit einer kleberlosen Anfasslasche (Fingerlift) hergestellt werden. Auch Vliese können auf diese Weise beschichtet werden und behalten dadurch ihre Atmungsaktivität und Durchlässigkeit.
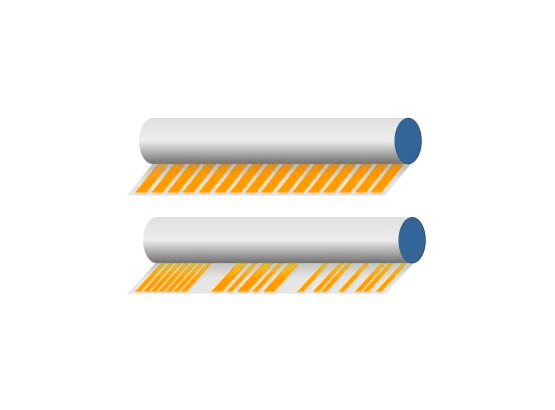
Häufig werden Beschichtung auf Polyesterfolie oder Teonex®- und Kapton®-Folie gewünscht. Jedoch können auch kundenseitig beigestellte Folien individuell streifenförmig beschichtet werden.
- Vollflächig bis zu 1.800 mm Breite
- Verschiedene Klebstoff-Arten und Auftragsstärken möglich
- Lösemittel- und Dispersionskleber einsetzbar
- Individuelles Muster der Streifen möglich, da Maske sehr flexibel erstellbar
- Sehr schmale und sehr breite Streifen möglich
- Einzelrollen mit ein- oder beidseitig kleberfreien Rand (z.B. für Fingerlift)
- Auch „Hosenträgerbeschichtungen“ möglich (zwei Klebestreifen aussen, mittig kein Klebstoffauftrag)
- Rollen verkleben nicht miteinander bei Lagerung übereinander (Lagerfähigkeit)
- Als Spleissklebebänder ohne die Gefahr des Ausblutens einsetzbar
Standardprodukt in verschiedenen Breiten und Folienstärken:
CMC 10262 Polyesterfolie mit Streifenbeschichtung (Lösemittel-Acrylatkleber)