Hier finden Sie unsere Wärmeleitfolien, -klebebänder, Silikonfolien und Gap-Filler: zu den Produkten
Wärmewiderstand, Wärmeimpedanz und spezifischer Wärmeleitwert
Wie wird Wärmeleitfähigkeit gemessen?
Wärmetransport als Funktion von Wärmeleitfähigkeit und Materialstärke
Wärmeleitung ist nicht nur eine Frage der verwendeten Materialien
Wichtige Überlegungen zur Wärmeleitfähigkeit kurz zusammengefasst
Messverfahren zur Bestimmung der Wärmeleitfähigkeit von Materialien (Elektrotechnik)
Warum ein schlechter spezifischer Wärmeleitwert kein Nachteil sein muss
Unterschied "Galvanische Trennung" und "Wärmespreizung"
Bedeutung von Grenzflächen für die Wärmeleitung in der Elektronik
Artikel: Warum Kühlung sich lohnt - Wärmeleitende Produkte für die Elektronik
Wärmewiderstand, Wärmeimpedanz und spezifischer Wärmeleitwert
In Datenblättern erhält man immer wieder unterschiedliche Angabe, wie wärmeleitfähig Materialien sind.
Gängig dabei ist die Angabe des spezifischen Wärmeleitfähigkeit, die dicken- und flächenunabhängig ein materialtypischer Wert ist: W/m*K
Doch auch Werte wie W/K oder K*in²/W sind zu finden. Wie rechnet man diese nun ineinander um (unter Vernachlässigung der Wärmeübergangswiderstände von einer Materialoberfläche zur anderen)?
Die Ausgangsgleichung lautet
Thermischer Widerstand = Stärke/ (Fläche * spezifische Wärmeleitfähigkeit)
K / W = d / (A * (W/m*K)) => K / W = d * (m*K/W) / A
Durch Umstellung der Formel nach dem jeweils gesuchten kann man leicht die Angaben aus verschiedenen Datenblättern vergleichen: zum Beispiel die Angabe K/W * d = K*in²/W (sofern man normiert auf Inch).
Als Faustformel: doppelte Materialstärke bei gleicher spez. Wärmeleitfähigkeit bedeutet die halbe Menge an Wärmetransport. Oder: bei gleicher Menge Wärme, die transportiert werden soll, muss ein doppelt so starkes Material auch eine doppelt so gute spez. Wärmeleitfähigkeit haben! Vorteil für dünne Folie wie Kapton MT+, selbst wenn der spez. Wärmeleitwert nur knapp 1 W/m*K beträgt.
Wie wird Wärmeleitfähigkeit gemessen?
Nach der ASTM D5470 wird die Wärmeleitfähigkeit eines Testmaterials wie folgt bestimmt: Ein beheizter Metallblock liefert die Wärmequelle. Getrennt durch das wärmeleitenden Material befindet sich darunter ein weiterer Metallblock, der als Wärmesenke (ggf. gekühlt) dient. Dicht über und unter dem wärmeleitenden Material sind Temperatursensoren angebracht.
Nachdem sich ein stabiler Wärmestrom eingestellt hat, wird die Temperaturdifferenz ermittelt, die durch das Testmaterial erzeugt wird. Daraus errechnet sich die Wärmeleitfähigkeit.
Vorteil dieser Methode gegenüber der Laserflash-Methode: auch die Rauigkeiten an der Oberfläche des Materials werden mit gemessen. Denn in der realen Einbausituation werden auch immer die Übergangswiderstände an den Schnittstellen der einzelnen Materialien eine Rolle spielen.
International anerkannte Normen zur Messung der spezifischen Wärmeleitfähigkeit sind u.a.:
ASTM E1530 und als Beschreibung einer möglichen Prüfmethode ASTM D5470
DIN EN ISO 22007 Bestimmung der Wärmeleitfähigkeit und der Temperaturleitfähigkeit von Kunststoffen
Wärmetransport als Funktion von Wärmeleitfähigkeit und Materialstärke
Es besteht ein direkter, linearer Zusammenhang zwischen der Materialstärke und dem Wärmestrom, der durch das Material hindurch transportiert werden kann.
Faustregel: Will man durch ein Material doppelter Stärke die gleiche Wärmemenge transportieren, muss die Wärmeleitfähigkeit ebenfalls verdoppelt werden.
Vorteil also für Kapton MT: sehr gute Wärmeleitfähigkeit bei geringer Materialstärke und sehr guter Spannungsfestigkeit
Wichtig dabei: diese Aussage bezieht sich nur auf den Transport innerhalb des homogenen Materials - der Wärmeübergangswiderstand ist dabei nicht berücksichtigt.
Wärmeleitung ist nicht nur eine Frage der verwendeten Materialien
Der Wärmeübergang z.B. von dem Gehäuse eines Leistungs-Transistors auf einen Aluminium-Kühlkörper kann recht schlecht ausfallen. Oberflächen-Rauigkeiten reduzieren die direkte Kontaktfläche, die für die Wärmeleitung notwendig ist, um etwa 20-40%.
Durch die Verwendung von z.B. Wärmeleitwachsen (PCM, Phase Change Material) kann man diesen Nachteil vermeiden. Das bei Raumtemperatur feste Wachs schmilzt bei der ersten Inbetriebnahme auf und füllt die Kavitäten aus. Der Wärmestrom kann ohne Unterbrechungen durch Lufteinschlüsse fliessen.
Die Lösung: Reduktion des Wärmeübergangs-Widerstands durch wärmeleitfähige Beschichtungen!
Wichtige Überlegungen zur Wärmeleitfähigkeit kurz zusammengefasst
Wichtig bei allen Überlegungen: in sehr vielen Fällen ist nicht die spezifische Wärmeleitfähigkeit (W/mK) entscheidend, sondern die Benetzungsfähigkeit (Formschluss), die Dicke (Wegstrecke für Wärmestrom) und die Querschnittsfläche des Wärmeleitpfades.
Elektronische Geräte werden immer kleiner und leistungsfähiger. Das stellt Entwicklungsingenieure vor immer größere Herausforderungen, denn auch die Lebensdauer elektronischer Geräte wird durch Wärme massiv beeinflusst. Die kompakte Bauweise vieler Elektronikbaugruppen und Vorgaben vom Design erfordern ein effizientes Heatmanagement. Wärmeleitende Silikonfolien, dünne, wärmeleitende Kaptonfolien und dicke, Toleranzen ausgleichende Gap-Filler sind dabei wesentliche Bestandteile neben den Kühlkörpern oder Heatpipes.
In den meisten Fällen werden die Produkte als Stanzteile benötigt. Dafür stehen Hub-Stanzen, Rotationsstanzmaschinen und Hochleistungs-Schneidplotter zur Verfügung. Von Stückzahl 1 bis in den Bereich von Millionen Stanzteilen.
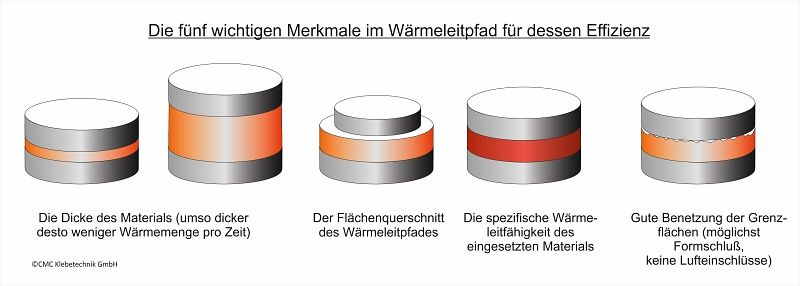
Scheinbarer Einfluss des Drucks auf die Wärmeleitfähigkeit
Sehr viele Datenblätter von Gap-Fillern oder wärmeleitenden Silikonfolien (TIM-Materialien) weisen eine merkliche Zunahme der Wärmeleitfähigkeit unter Druck aus. Der Grund dafür ist jedoch nicht, dass die wärmeleitenden Partikel in der Trägermatrix besser aneinander gepresst werden.
Wie jeder andere Festkörper oder Flüssigkeit sind auch diese Produkte nicht komprimierbar. Anders wie bei Schäumen enthalten wärmeleitende Produkte möglichst wenig Lufteinschlüsse.
Die Verbesserung der Wärmeleitfähigkeit erfolgt vor allem durch einen unter Druck besseren Formschluss zwischen den Fügepartnern (z.B. Gehäuse eines Leistungsmoduls und Kühlkörper mit TIM-Material dazwischen). Die mehr oder weniger weichen Produkte dringen in die Oberflächenrauigkeit ein und verdrängen die eingeschlossene Luft und erhöhen die Kontaktfläche. Diese Kontaktfläche ist der Leiterquerschnitt für den Wärmestrom (analog der dem Kupferquerschnitt beim elektrischen Strom).
Ein zusätzlicher Effekt tritt bei weicheren Materialien durch das Verdrängen aus dem Druckbereich heraus ein. Die Dicke des Materials (z.B. Gap-Filler in 4 mm bei 10 bar nur noch 2 mm) reduziert sich dadurch und der Wärmestrom kann sich dadurch erhöhen.
Tatsächlich ändert sich aber nicht die materialspezifische Wärmeleitfähigkeit, sondern in der Formel für den Thermischen Widerstand ändern sich die beiden anderen determinierenden Parameter: Länge und Querschnittfläche
Rth = l / (A *λ)
Dieser Effekt ist also für kleine Bauteile durchaus vorhanden - sind die Flächen jedoch groß, kann nicht mit Druck eine über die verbesserte Anpassung des Materials an die Fügepartner (Benetzung) hinaus gehende Reduktion des Wärmewiderstands erzielt werden!
Messverfahren zur Bestimmung der Wärmeleitfähigkeit von Materialien (Elektrotechnik)
Die Ermittlung eines spezifischen Wärmewiderstandes kann mit mehreren verschiedenen Messverfahren erfolgen. Diese sind für homogenen Materialien genauso einsetzbar wie für mehrschichtig aufgebaute Systeme geeignet. Allerdings ist ihre Praxisrelevanz unterschiedlich.
-
In vielen Elektronik - Entwicklungsabteilungen wird vergleichend gemessen. Bei dieser sehr praxisnahen Messmethode wird ein Leistungstransistor verwendet, der mit einer bestimmten und geregelten Leistung beaufschlagt wird. Mit z.B. PT100-Messfühlern wird die Temperatur z.B. des Gehäuses nahe an dem Halbleiterkristall ermittelt und bei verschiedenen Wärmeleitmaterialien verglichen.
-
Ein standardisierter Test mit guter Praxisnähe ist ASTM D5470. Bei diesem Test wird zwischen zwei Metallzylindern das zu prüfende Material eingelegt. Die Kontaktflächen sind poliert und sollen so größtmögliche Kontaktfläche bieten. Es wird ein stabiler Wärmestrom eingestellt und die Differenztemperatur ermittelt, die an den Grenzflächen des Probenmateriales entsteht. Durch Anpassung des Drucks, mit dem die beiden Metallzylinder die Probe komprimieren, kann die Wärmeleitfähigkeit zusätzlich in Abhängigkeit der Kompression ermittelt werden. Mit dieser Methode kann man auch kombinierte Produkte (z.B. beschichtete Folien) gut charakterisieren.
-
Bei der Laserflash Methode (z.B. ASTM E1461) wird die Probe von unten mit einem Laserimpuls erwärmt, während man auf der anderen Seite die Sprungantwort misst. Diese Messmethode ist sehr schnell.
Nachteil: die Messung berücksichtigt nahezu überhaupt nicht Oberflächenstrukturen. So kann im Extremfall z.B. ein hartes Keramikmaterial eine hervorragende Leitfähigkeit, mangels Anpassung an Oberflächenrauigkeit jedoch einen sehr hohen Übergangswiderstand besitzen. -
Die 3-Omega-Methode wird mittels Heizdraht eine oszillierende Wärmewelle in die Probe geschickt. Die als Antwort auf die Anregung gemessene Wechselspannung bei dreifacher Anregungsfrequenz lässt sich umrechnen in die spezifische Wärmeleitfähigkeit. Die Methode ist gut für dünne Schichten geeignet. Sie wird jedoch selten in der Praxis angewendet.
-
Eine weitere Messmethode ist das „Hot-Disk“ Verfahren (DIN EN ISO 22007-2), bei dem ein Sensor zwischen zwei identische Scheiben des zu messenden Material mit einer konstante Aufheizrate erhitzt wird. Die Erwärmung des umgebenden Probekörpers ist ein Maß für die Wärmeleitfähigkeit.
Warum ein schlechter spezifischer Wärmeleitwert kein Nachteil sein muss
Im Allgemeinen vergleicht man zunächst die in Datenblättern gerne hervorgehobenen spezifischen Wärmeleitwerte in W/m*K. Doch dieser Wert ist nur ein erster Anhalt bei der Auswahl des geeigneten TIM-Produktes.
Neben Fragen wie
-
der Notwendigkeit galvanischer Trennung,
-
des verfügbaren Bauraums,
-
dem thermisch-dynamischen Verhaltens im Betrieb (Lebensdauerbetrachtung) oder
-
dem Ausgleich von Fertigungstoleranzen
sind die sogenannten Übergangswiderstände und die Materialdicke entscheidende Faktoren. Sie bestimmen bisweilen wesentlich die Effizienz einer Entwärmungsmaßnahme.
Bezüglich der Einflüsse des Wärmeübergangswiderstandes finden Sie hier nähere Erläuterungen.
Paxisbeispiel: Schaut man sich einmal eine Burgwand an, dann ahnt man, was damit gemeint ist, dass die Materialdicke einen Einfluß hat auf den Wärmetransport. Es dauert lange, bis Wärme oder Kälte durch eine so dicke Wand dringt (einschließlich der spezifischen Wärmekapazität). Im Gegensatz dazu ist eine Zeltwand nahezu sofort von Wärme oder Kälte durchdrungen.
Normiert man die Fläche einmal zu 1 (m², cm², inch³…), so erscheint in der Berechnungsformel für den Wärmewiderstand
Rth = l / (λ * A) -> nur noch der Term l / λ
Anhand einiger typischer Produkte aus dem Wärmemanagement kann man nun den Vergleich herstellen zwischen Produkten mit guter spezifischen Wärmeleitfähgkeit und großer Materialstärke im Vergleich zu z.B. Kapton® MT Folie mit vergleichbar schlechter spezifischer Wärmeleitfähigkeit.
Material | Stärke in mm | Spezifischer Wärmeleitwert | Wärmewider-stand (normierte Fläche) |
MP 7016-020D, PCM |
0,015 | 1,0 | 0,015 |
CMC 15811 trägerlos AC |
0,020 | 1,0 | 0,02 |
CMC 15005, Silikon-Folie |
0,200 | 5,0 | 0,04 |
CMC 73250, Kapton® MT |
0,025 | 0,45 | 0,06 |
TF 5320F, Acrylat |
0,200 | 3,3 | 0,06 |
TR-5912F, trägerlos, AC |
0,125 | 1,1 | 0,11 |
CMC 73550, Kapton® MT |
0,050 | 0,45 | 0,11 |
CMC 15020, Silikon-Folie |
1,00 | 5,0 | 0,2 |
TR 5925F, Acrylat |
0,250 | 1,1 | 0,23 |
CMC 15014, Silikon-Folie |
3,00 | 2,0 | 1,5 |
Folgerung: Wie man leicht erkennt, haben ein dicker Werkstoff mit guter spezifischer Wärmeleitfähigkeit und eine relativ schlecht wärmeleitende Kapton Folie mit sehr geringer Dicke den gleichen Thermischen Widerstand pro Flächeneinheit.
Das mit 2 W/m*K über vier Mal besser leitfähige Material im Vergleich zu Kapton MT hat dennoch einen höheren Wärmewiderstand, da es deutlich dicker ist (3 mm).
Beispiel: Wärmeleitad aus gefülltem Silikonmaterial
Unterschied "Galvanische Trennung" und "Wärmespreizung"
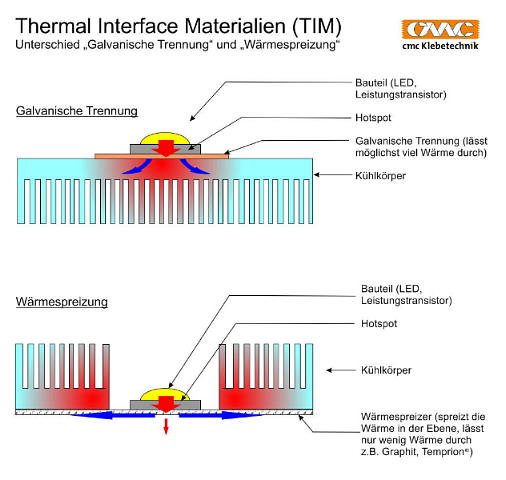
Bedeutung von Grenzflächen für die Wärmeleitung in der Elektronik
Jeder, der schon mal mit wärmeleitenden Materialien in der Elektronik zu tun hatte, kennt das Phänomen. Mit zunehmendem Druck verbessert sich die Wärmeleitfähigkeit. Dies jedoch nur damit zu erklären, dass die wärmeleitfähigen Partikel innerhalb der tragenden Matrix (Polyimid, Silikon, Acrylat, etc.) näher zusammen gedrückt werden, erklärt nur die halbe Wahrheit.
Die meisten thermisch leitenden TIM-Materialien (Thermal Interface Materials) werden hergestellt aus einem Trägerwerkstoff, der elektrisch nicht leitend ist. Denn meistens wird eine galvanische Trennung benötigt – Graphitfolien oder Metallfolien bilden die Ausnahme da, wo es nicht auf eine elektrische Trennung ankommt.
Leider sind die üblichen elektrischen Isolierwerkstoffe schlechte Wärmeleiter. Deswegen muss man in die Polymermatrix wärmeleitenden Partikel einbringen. Umso mehr, desto besser die Wärmeleitung. Allerdings verändert man dabei erheblich die Gefügestruktur innerhalb des Werkstoffes. Ehemals gut miteinander vernetzte Polymerketten verlieren ihre Verbindung zueinander, der Werkstoff wird brüchig und mechanisch immer instabiler, Folien reißen bei geringer Zugbelastung, die Spannungsfestigkeit verringert sich.
Es gibt also eine Obergrenze, ab der massiv die physikalischen Eigenschaften unter der Zugabe weiterer wärmeleitfähiger Zuschlagstoffe leiden (z.B. auch Fließfähigkeit von Tränkharzen). Das führt in der Praxis dazu, das selbst hochgefüllten Systemen kaum Wärmeleitwerte über 10 W/mK erreichen.
Der optimale Fall, dass die Wärmeleitung hauptsächlich durch direkte Berührung von wärmeleitenden Partikeln wie Aluminiumoxyd, Bornitrit oder Aluminiumnitrit erreicht wird, ist also eher theoretisch. Vielmehr verkürzen die Zuschlagstoffe für den Wärmestrom den Weg durch den ansonsten schlecht wärmeleitenden Polymerwerkstoff.
Durch Zusammenpressen kann man in geringem Maße vor allem bei silikon- oder acrylatbasierenden Gapfillern (Spalten-Füller) eine oft nicht unerhebliche Verbesserung der Wärmeleitfähigkeit erreichen. Allerdings sind diesem Zusammenpressen enge Grenzen gesetzt. Zudem belastet eine solche Krafteinwirkung z.B. aktive Bauteile und Platinen.
Oft vernachlässigt in der Betrachtung aller Bestandteile eines Wärmeleitpfades sind die thermischen Widerstände ZWISCHEN den einzelnen Fügepartnern. Denn selbst eine Kombination aus den Metalloberflächen zweier Bauteile (Transistorgehäuse, Aluminiumkühlkörper) wird nicht die theoretisch mögliche Wärmeleitfähigkeit von z.B. Stahl oder Aluminium erreichen. Die mikroskopisch rauen Oberflächen erreichen keinen 100%ige Formschluß. So geht ein Teil des Querschnittes für den Wärmestrom verloren, der Wärmewiderstand erhöht sich an der Grenzfläche erheblich (Luft).
Wie aber erreicht man einen Formschluss für bestmöglichen Wärmetransport?
Durch Maßnahmen wie Schleifen und Polieren, also sehr glatter Metalloberflächen, könnte man eine Verbesserung erzielen. Doch bei kostengünstig hergestellten Serienteilen ist ein solcher Aufwand nicht realisierbar. Zusätzlich sind Schwankungen innerhalb von mechanischen Toleranzgrenzen nicht vermeidbar. Schließlich verändert sich die Auflagefläche im realen Betrieb auch noch durch unterschiedliche Ausdehnungskoeffizienten, die sogar zu konkaven und konvexen Verwölbungen führen können.
Ein seit Jahren gängiges Verfahren ist das Aufbringen einer geringen Menge Wärmeleitpaste. Diese oft, aber nicht immer silikonbasierenden Pasten sind hoch angereichert mit fein gemahlenen Werkstoffen, die wärmeleitend sind (meist Aluminiumoxyd). Dünn aufgetragen fliessen sie unter Druck und Wärme in die Spalten der verschiedenen Oberflächen und gleichen im Idealfall gerade so die Maßtoleranzen, Folgen thermischer Ausdehnung und die Oberflächenrauigkeit aus. Aufgrund der pastösen Konsistenz besteht jedoch durchaus die Gefahr der Überdosierung. Ausserdem neigen solche Wärmeleitpasten dazu, bei wechselnder thermischer Belastung unter der Kontaktfläche auszupressen (pump-out), auszubluten (bleeding) oder auszutrocknen (dry-out).
Besonders in Bezug auf eine immer gleiche Dosierung helfen trägerlose Filme aus sogenanntem Phase-Change Material (PCM) mit klar definierter Materialstärke.
Was sich so mystisch anhört ist technisch gesehen ein Material, das bei Raumtemperatur ein fester Film ist, das jedoch bei Erwärmung über eine Sprungtemperatur (meist 50 – 60°C) erweicht, also seine Phase, seien Zustand ändert. Das Material wird von CMC Klebetechnik entweder als Beschichtung auf Folien oder auf einer transparenten Trägerfolie angeboten. Es verhält sich nach dem ersten Aufwärmen (burn in) wie Wärmeleitpaste: sie füllt in erweichter Form die Kavitäten in den Oberflächen aus, verdrängt dabei den schlechten Wärmeleiter Luft und gleicht auch später geringe Maßtoleranzen aus.
Im erkalteten Zustand ist das Material fest, allerdings ohne große Haftkräfte. So kann im Servicefall eine solche Verbindung geöffnet werde. Sobald die beiden Bauteile wieder zusammen gebaut sind und sich erwärmen, schmilzt das Phase-Change-Material (PCM) erneut und füllt die Grenzfläche formschlüssig aus. Der Wärmeleitpfad ist also auch nach mehrmaligen Öffnen und Schließen weiterhin funktionsfähig.
PCM Lösungen von CMC Klebetechnik
CMC Klebetechnik verwendet ein Hochleistungs-PCM, das bis zu 180°C eingesetzt werden kann und dabei nicht ausblutet oder austrocknet. Der wärmeleitende, trägerlose Film kann zwischen ca. 15µm und 50µm Stärke hergestellt werden. Größere Stärken (Gap-Filler) werden nach anderen Verfahren hergestellt und sind dann nahezu immer auch elektrisch isolierend.
Messungen und praktische Erfahrungen vieler Kunden bestätigen, dass Phase-Change-Beschichtungen den Wärmewiderstand eines Wärmepfades drastisch reduzieren können. Anstatt durch teure mechanische Bearbeitung Oberflächen zu glätten oder durch Einsatz höher wärmeleitfähiger Werkstoffe die Konstruktion zu verbessern, sollten Elektronik-Entwickler immer auch die Grenzflächen im Auge behalten. Und diese lassen sich bei Metallen nicht durch Zusammenpressen mit wenigen Bar verändern. Anders bei zum Beispiel relativ steifen Isolationsfolien oder Gap-Fillern mit hoher Härte. Diese profitieren von Beschichtungen mit PCM-Material, das die Benetzung der Oberflächen unter Druck verbessert.
Solche wärmeleitenden Isolationsfolien werden eingesetzt, um bei geringer Materialstärke (kurzer Wärmepfad) hohe Spannungsfestigkeiten zu realisieren, wohingegen Gapfiller vor allen Spalten, Toleranzschwankungen und unterschiedlich hohe Bauteile thermisch an eine Wärmesenke anbinden. Eine Vielzahl unterschiedlicher Lösungen wird von CMC Klebetechnik, zum Teil in Verbindung mit wärmeleitenden Kleberbeschichtung oder PCM-Beschichtungen angeboten.
Ein Gedankenspiel zur Verdeutlichung:
Ein Aluminiumklotz mit der Fläche A=1 und eine Wärmeleitfähigkeit von 230 W/mK liegt auf einem gleichartigen Aluminiumklotz, ebenfalls mit der Fläche 1.
Bei einer durch Oberflächenrauhigkeit reduzierten Kontaktfläche von 50% ergibt sich folgende Situation:
Rth am Grenzübergang ist eine Parallelschaltung der Wärmewiderstände von Aluminium (230W/mK) und Luft (0,0262 W/mK).
Setzt man die Wärmeleitfähigkeit der Luft zu Null, halbiert sich der zur Verfügung stehende Wärmepfad-Querschnitt. Füllt man den Spalt jedoch mit einem Phase-Change-Material von z.B. 5 W/mK aus, erhält man einen deutlich reduzierten Wärmeübergangswiderstand {Rth = l / (λ*A)} der Schnittstelle, da die gesamte Fläche ausgenutzt (benetzt) wird und das PCM-Material fast zweihundertmal besser Wärme leitet wie Luft.
Wärmeübergangswiderstand an Grenzflächen OHNE vermittelndes Phase-Change-Material