Modern wide-bandgap (WBG) power semiconductors generate significantly more electrical stress for insulation materials than classic silicon power transistors. The advantages of reduced power loss in the power modules are offset by increased stress on the external insulation system.
Classic insulation products are tested with sinusoidal AC voltage at low frequency (50 Hz). Enameled wires are tested together with stress factors such as increased thermal stress, repeated temperature change cycles, vibration and in contact with other insulating materials. This results, for example, in minimum requirements for the insulation thickness.
Wide-bandgap transistors (silicon carbide SiC, gallium nitride GaN, possibly also InGaN) have several advantages due to their particularly wide gap between the valence band and the conduction band: they can be used at higher voltages, enable higher switching frequencies and higher operating temperatures. Due to the lower power loss, a more compact design and higher power density is possible. Although the production of the base materials (ingots) is much more expensive, the long-term advantages in applications such as servo drives or traction motors put this additional cost into perspective. Modern drive motors for vehicles in particular benefit from the compact design of the controlling frequency inverters.
Application technology
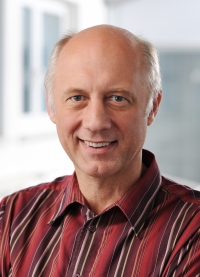
If you have any questions, please contact:
Gerald Friederici
Phone: +49 6233 872 356
E-Mail: friederici (at) cmc.de
However, with higher voltages and, above all, higher frequencies, stress phenomena occur that previously did not have to be taken into account to the same extent. In addition to the additional heat load caused by increasingly compact designs, there are the high voltages used to keep the current-related copper content in inductive components as low as possible. High voltages, in conjunction with the almost unavoidable phase boundaries between current-carrying components and ambient air, lead to the risk of sliding or corona discharges. These can occur in encapsulated coils at cavities contained therein, but also, for example, at connecting cables and conductor transitions.
In addition to the risk of partial discharges occurring due to the high operating voltages (and overshoots during fast switching operations), the high alternating frequency of the half-bridge or full-bridge control by WBG power transistors contributes to stressing the insulation materials themselves. The harmonics also play a significant role in this electrically induced stress, as they can even reach the MHz range.
With every change in polarity, polar components in the insulation material are repolarized (dielectric polarization). Similar to a capacitor, the insulation material behaves like a frequency-dependent resistor in the alternating field. The steep dU/dt edges and short signal times in the PWM process cause the insulation material to heat up considerably. As temperature is the most important cause of ageing for the vast majority of insulation materials, this internal self-heating also shortens the service life. The breakdown voltage, which is also temperature-dependent, is also significantly reduced depending on the material and frequency. High direct voltages with superimposed alternating voltage ripple are also particularly critical, as direct voltages (DC) involve additional mechanisms such as electrochemical migration. The AC voltage losses in the material plus the high DC voltage potential favor ion migration on or through the material.
The advantages of lower heat loss generation in the WBG power transistors themselves are therefore offset by increased ageing of the insulation materials due to heat, electrical stress and partial discharges.
In the vast majority of cases, enameled wires are used in inductive components. Depending on the wire diameter and voltage load, the minimum layer thickness of the wire enamel is defined in various standards. However, most standards do not yet take into account the relatively new and less common SiC and GaN power transistors and their possibilities.
In special applications such as traction motors for vehicles, extreme climatic situations can lead to sudden changes in temperature. On a cold winter's night in northern Europe, the winding of a motor can cool down to below -20°C. If power is suddenly called up from this motor, the winding heats up abruptly - with the result that the paint insulation can be damaged.
Even the breakage of a few layers of paint increases the risk of partial discharges, as the much less insulating ambient air now takes over the task of the insulating paint. As a countermeasure, armature rods of e.g. traction motors can be wrapped with a suitable insulating foil in addition to the paint insulation. Although this reduces the possible copper fill factor, it dramatically increases the level of safety. Because foils such as Kapton® CRC (polyimide polymer with inorganic filler) are specially designed to withstand the effects of partial discharges for a long time. The film therefore not only acts as additional insulation, but above all as protection against the consequences of PD.
There is another reason to produce wire conductors with wrapped foil insulation: Stranded wires.
At high currents or high frequencies, current displacement or the skin effect occurs. This reduces the available conductor cross-section and increases the resistance (loss), as the charge transport is limited to the surface. To counteract this effect, a thick wire is divided into many thin copper filaments, which together have a much larger surface area. The individual, thin stranded wires do not require a high insulation barrier due to the low differential voltage between them. However, the stranded wire itself must be insulated if it is to be used in an inductive component, for example.
Differential layer voltages and high voltage potentials between stranded wire and earth require good external insulation in modern frequency converter-driven electric motors. This can be achieved with spirally wrapped insulation foil.
Even at low layer thicknesses, products such as CMC 70100 (Kapton® insulation tape with acrylic adhesive) provides excellent insulation and is very easy to install.
The adhesive used allows a certain amount of movement, but prevents excessive displacement of the overlaps of the spiral winding. Kapton® also has an excellent power reserve in the event of a fault, even with a class F or class H insulation system.
As with solid copper wires (e.g. hairpin windings in traction motors), Kapton® CRC (CMC 70300, Kapton® CRC adhesive tape with high-performance acrylate adhesive) also provides excellent resistance to partial discharge phenomena.
The use of foil-wrapped wires and strands is an essential additional protection against electrical stress and its consequences, especially when using high-frequency wideband-gap transistors. CMC Klebetechnik has been supplying such winding foils to litz wire manufacturers for two decades.
DC voltage and insulation failure in high-voltage powertrains