CMC Klebetechnik manufactures die-cut parts from well over 300 different film-like materials. The very extensive machine park makes it possible to realize economical production from the smallest quantities up to several million pieces. We specialize in technically demanding, high-quality materials such as Polyester film, Nomex®, Kapton®, metal films such as copper and aluminum or corresponding laminates made from them.
The customer has the advantage that, on the one hand, he is talking to a competent partner when it comes to die cutting , but who also provides additional support in product selection. If a specific material does not yet exist, it is often possible to use the Development a proprietary combination of film and Coating to find a solution. CMC Klebetechnik offers the entire vertical range of manufacture for this purpose, from material procurement to coating and cutting to die cutting.
Adhesive die cut parts are ubiquitous in our daily lives. This is because manufacturers often have to think about how to bond different materials together, fit accurate insulation in electrical devices, and cover sensitive surfaces. All of these applications can be simplified by using molded stampings in manufacturing. That's because die cut parts are pass accurate, always the same gauge, and save assembly time.
CMC Klebetechnik manufactures on over a dozen different die cutting machines for customized solutions. We have the machine technology, the experience with hundreds of different materials and the personnel to offer you a suitable solution. The materials we use are not limited to our own products. We also manufacture as a contract service provider from your provided material. We use our own materials or films, fabrics or nonwovens specified by the customer. Lifting die-cutting machines, rotary die-cutting machines, cutting plotters or cross cutters and laminators enable the economical production of small and large series.
Advantages
-
Film die-cuts can make manufacturing operations faster, cheaper and easier
-
Die-cut parts are preformed, precisely metered, generate no waste and save assembly effort
-
individual die-cut parts are already tailored to fit the need
-
Recesses enable precise fixation
-
folds an adaptation to the required geometry
-
Adhesive surfaces a fixation of the die-cutting part
We have all the possibilities to economically produce die cut parts from quantity 1 up to very large quantities. Depending on the material, the material thickness can be between 5 µm (films) and about 3 mm (sheets ).
Die-cut parts
The use of self-adhesive die-cut parts results in significant material and assembly time savings in a number of assembly operations. We produce shaped die-cut parts from all film-type materials according to your specifications - on rolls, as sheets and as individual parts. Aids such as touch tabs or butterfly folding are possible. We die-cut a wide variety of materials in our company. According to your specifications, we produce between 100 and about 10 million die-cut parts - from stamp size up to about 500 x 500mm.
Technical capabilities:
- Prototyping, pre-series production or small batches
- Rotary die cutting machines for large series
- Stroke die cutting for parts from a few mm² to approx. 0.3m²
- Cutting plotter
- Printing units for UV coating
- Laminating, cross cutting (cutting to length), folding
- 3D molded die-cut parts, customized die-cut parts
- Contract punching
- adhesive on one or both sides
- single-lane or multi-lane on rollers
Die-cutting tools
Different tools are used in our company for the production of die cutted parts .
In the simplest case, we use die cutting tools called "strip steel cutting tool". Here, a thin knife steel is embedded in a tool carrier (wooden plate, pertinax plate). The shape of this knife line corresponds to the die cutted part.
Such tools are inexpensive and sufficient in most cases. Tolerances of up to +- 0.3 mm and medium quantities of up to approx. 200,000 parts can be achieved with them.
Full-cutting tools are used when a longer service life (number of die cutted parts) is required, greater accuracy is demanded or, for example, 3D cuts or die cut in hard materials is required. These tools, some of which are very heavy, with elaborate cutting edges/shapes often cost several thousand euros. We die cut all materials manufactured in our company, but also many other products according to your drawings.
For high quantities high requirements and thin to very thin material (max. some 1/10 mm) the use of rotary die cutting machines can be a reasonable alternative. This continuous die cutting process (the die cutting knife is a roller) makes it possible to produce large quantities cost-effectively with the appropriate materials.
For very large parts we use our modern cutting plotter. On it, we can produce the desired die-cutting part directly from the electronic drawing. The cutting plotter has a working area of approx. 2,000 x 3,000 mm. We are also happy to advise you on the choice of materials to be used. Often cheaper alternatives are possible.
Film die cutting parts - production and materials used
The fact that die cutted parts have advantages in many industrial sectors (see article "Variety of stamped parts"), has been known for a long time and is used abundantly. But how are die-cut parts actually made from films, fabrics or paper ? The following insights into production at CMC Klebetechnik explain a little about how molded die-cut parts are created.
At the beginning there is an idea. Some technical product (e.g. shut-off valve, servo motor, grinding pad for eyeglass lenses, blood glucose measuring strip) is to be produced. At some point during the design or development of this technical product, a work step can only or best be solved with a die-cut part (e.g. sealing ring in shut-off valve, insulation foil in the winding head of the servomotor, laminate of cover foils and functional carrier in the blood glucose strip).
Together with the technical drawing, the requirements profile for the stamped part is created. What loads must the material withstand, how precisely must the contour be maintained, in what way should the molded part later be available in production?
Together with the experts at CMC Klebetechnik, a combination of design specifications for the label, die-cut or molded part and other requirements is created. The result is a customized solution that incorporates manufacturing experience and, above all, the wide range of possible materials.
CMC Klebetechnik uses as a basis for punched parts from foils and fabrics for example:
-
Kapton® HN Polyimide Films
-
Nomex® 410 Aramid Papers
-
Mylar® A polyester films
-
Hostaphan® RN polyester films
-
EPDM foams
-
Crepe paper adhesive tapes
-
PTFE foils
-
Polycarbonate films
-
Self-adhesive glass fabric
-
Teonex® films
-
PPS, PEI, PES or PEEK high-conductivity films
-
FEP foils
-
Acetate silk fabric
-
Laminates from different products
-
....and much more
Adhesives and coatings
Of course, most of the starting materials for stamped parts can also be given a self-adhesive finish. For this purpose, CMC Klebetechnik uses adhesives of industrial standards. Depending on the application, they can be modified to achieve specific properties. In the case of paint protection labels, for example, the die-cut part should be removable without leaving any residue after the paint has been applied and dried, in order to make a type plate visible again, for example.
Adhesives used by CMC Klebetechnik:
-
synthetic rubber adhesives (e.g. good immediate adhesion, partly removable, ageing resistant)
-
Acrylic adhesives (e.g. good to very good adhesive strength, very resistant to aging and UV-stable)
-
Polysiloxane adhesives (e.g. highest temperature resistance, extreme aging resistance, use indoors and outdoors)
-
Heat-seal adhesives (melt when temperature is added and then have good adhesive forces, coating possible on almost all materials)
-
Laminate adhesive, hot melt adhesive
-
Mixed adhesives and other customized adhesives
Manufacturing techniques for the production of molded stampings
At CMC Klebetechnik, the production of die-cut parts from films, foams and fabrics is based on four basic manufacturing techniques:
-
Stroke punching with strip steel cutting tools
-
Rotary die-cutting with full-cut cylinders or die-cutting plates
-
Formatting and cutting to length
-
Cutting plotter for quantities from "one piece" molded part
Initial samples/ sample die cut parts - rapid prototyping in series production quality
Our state-of-the-art flatbed plotters enable very precise sampling with die-cut parts within a very short time.
With a maximum part size of 2,270 x 3,200 mm, accuracies of up to +/- 0.1 mm can be achieved and materials up to 10 mm thick can be processed.
Due to the many different base films processed at CMC Klebetechnik, almost all common film types processed in the industry are available.
These are among many others for examplePolyester films,Nomex Aramid Paper,Kapton films,PTFE-andETFE filmsas well as many other special films and technical fabrics.
The films can be self-adhesive or can also be processed as a laminate, e.g. with copper films, to form die-cut parts (molded die-cut parts).
This gives them the opportunity to comparatively test different materials as early as the prototyping phase of a new development. And in series production quality. With a contour that can be changed at any time.
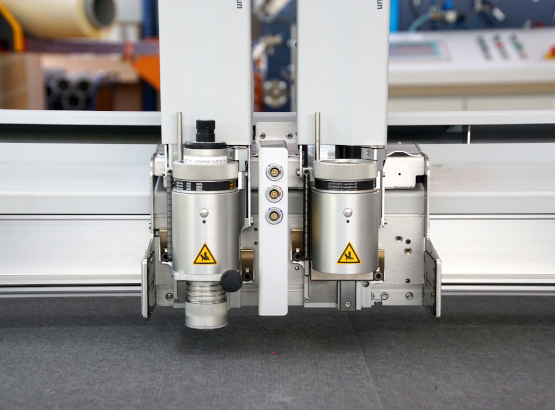
More articles on the subject: Die cutting/ Shape die cutting part
Assemble non-adhesive die-cut parts on rolls
Every die cutter knows the two problems with die cut parts made of non-adhesive material: How do I get the individual parts out of the die area? And how do I "pack" molded parts so that they can be easily processed further?
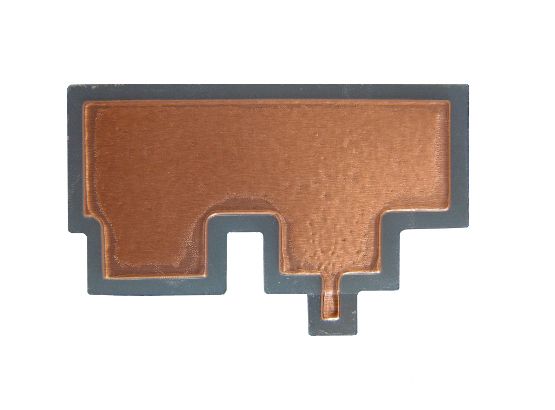
Die cutted parts for EMC shielding
For years, the trend in electrical engineering has been unbroken to develop ever smaller, more powerful and more intelligent devices. Until a few years ago, the performance of today's smartphones was reserved for desktop computers.
Variety: Die-cut parts from foils