Generally known conditions for good bonding are:
the surface of the substrate to be pasted must be free of grease and dust and dry.
strong pressing during bonding increases the adhesive force.
But this still does not explain why "bonding" takes place at all. The molecular forces of attraction that build up are essential for bonding between two different materials, because in very few cases does a chemical bond occur. Atomic bonding forces and, often to an even greater extent, polar forces of attraction are decisive. Similar to a magnet, such polar molecules attract each other and thus influence the strength of the bond.
A measure of the polarity of materials is the surface energy. Particularly polar surfaces are also referred to as high-energy surfaces. Adhesive tape therefore adheres better to high-energy surfaces than to low-energy surfaces. This wettability is measured in dyn/cm (mN/m).
Energetically different surfaces can be illustrated by the difference between a drop of water on a waxed and unwaxed paint surface:
The untreated coating is highly energetic, which strongly attracts the polar water molecules: The water drop runs wide and becomes a large-area puddle. The situation is different with waxed varnish: here the surface energy is low and, accordingly, the binding force between the water molecule and the substrate is low, the water drop remains small, spherical.
Guide
1 Basic differences in adhesives
1.1.1 Insulation class E (up to 120°C)
1.1.2 Insulation class B (up to 130°C)
1.1.3 Insulation class F (155°C)
2 Properties of adhesive tapes
2.1 Tensile strength/tear force
2.2 Elongation at break
2.3 Burning behavior
2.4 Electrolytic corrosion effect
2.5 Rolling force
2.6 Shear strength
2.7 Dielectric strength
2.8 Adhesive strength
2.9 Creepage distance formation
2.10 Chemical compatibility, insulation systems
This illustration leads to the conclusion that adhesive formulations must be matched to the surfaces to which the adhesive is to adhere later. An adhesive can adhere well to a high-energy surface, while it adheres almost not at all to siliconized paper - but also vice versa.
Examples of high-energy (polar) plastics are:
Polyvinyl chloride PVC (approx. 39 dyn/cm)
Polycarbonate PC (approx. 46 dyn/cm)
Polyuretane (approx. 43 dyn/cm)
Polyimide. e.g. Kapton (approx. 41 dyn/cm)
Polyester PET (approx. 41 dyn/cm)
Examples of low-energy (non-polar) plastics include:
Polypropylene PP (approx. 29 dyn/cm)
Polytetrafluoroethylene PTFE (approx. 18 dyn/cm)
Silicones (approx. 24 dyn/cm)
Polyethylene PE (approx. 31 dyn/cm)
Of course, other factors also play a role in bonding. For example, the anchoring of the adhesive to irregularities or the adhesion mediation by so-called primers (these mediate as a very thin layer between the surface and the adhesive). In most cases, adhesives also consist of mixtures of polymer base materials, oils and resins. These are mixed and adjusted depending on the application.
It is beyond the scope of this guide to list all the components that influence bonding.
1 Basic differences in adhesives
Adhesives join parts by means of cohesion (internal bond of the adhesive) and adhesion (surface adhesion). In some adhesives, the proportion of cohesion predominates, and vice versa. The following two pictures are intended to illustrate the different influences on bonding:
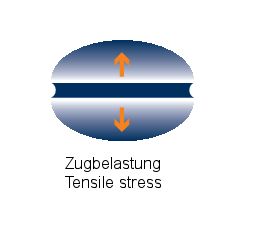
Adhesion, high instantaneous tensile strength, good flow properties, but low shear strength (low internal strength of the adhesive cannot withstand shear stress).
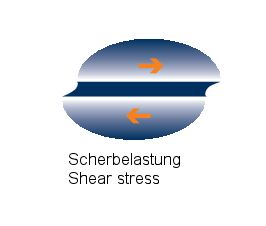
Cohesion, high shear strength, no creep or cracking of the adhesive, but possibly low adhesion on uneven surfaces (poor flow properties, poor wetting).
Particularly unfavorable loads for bondings are splitting and peeling loads. In this case, not the entire surface is loaded, but only one line. This can cause the adhesive film to tear at this point (cohesion fracture within the adhesive or adhesion fracture between adhesive-substrate interfaces).
Another difference between adhesives with a high adhesion content (rubber adhesives) or a high cohesion content ("dry", shear-resistant acrylic adhesives) is their ability to penetrate the roughness of the surface to be bonded.
Heat-curing adhesives on adhesive tapes mostly have the advantage of good flow properties before curing and excellent shear strength after heating. In addition, they usually retain an elastic state, i.e. they do not become brittle or harden (exceptions are e.g. epoxy resins).
1.1 Classification of insulation materials according to thermal classes (IEC 60085)
Components and devices in which insulation films and adhesive tapes are used in production are often subject to a wide variety of environmental conditions. This also includes a high ambient temperature or additional self-heating. Therefore, insulation tapes are divided into so-called thermal classes.
In principle, these thermal classes specify which minimum properties (tensile strength and/or tensile strength or weight loss) specified in IEC 60454, for example, an insulating adhesive tape must still have after 20,000 hours of operation. This classification enables the developer to select materials for a specific application without having to conduct his own lengthy tests.
Based on this classification of films, adhesives can also generally be assigned to thermal classes:
1.1.1 Insulation class E (up to 120°C)
Rubber adhesives are frequently used in this class. This adhesive consists of natural or synthetic rubber compounds which, through the addition of resins and fillers, produce a tacky, impregnant-resistant and, to a certain extent, shear-resistant bond. The adhesive is inexpensive and has a particularly high initial tack.
However, these adhesives age and have only a low cohesion of the adhesive mass (cohesion).
1.1.2 Temperature class B (up to 130°C)
Polyester films that can withstand a short-term load of 175°C are very frequently used in this class. The most commonly used adhesive system for this temperature class is acrylic adhesives.
They are chemically very resistant. Thanks to their UV and aging resistance, acrylic adhesives can also be used outdoors. A wide range of adhesive settings are possible by adding resins and crosslinkers.
In addition, solvent-free, water-based acrylic adhesives are available today, so that environmentally friendly production is possible. However, dispersion adhesives are only used to a limited extent in electrotechnical applications because of their electrolytic corrosion effect.
For thermal class B, there are also numerous synthetic rubber adhesives that can be used. However, they have now been largely displaced by acrylate adhesives.
1.1.3 Insulation class F (155°C)
Both types, thermosetting acrylic adhesives and thermosetting rubber adhesives are used in this area. However, due to the increased temperature load, an acrylate adhesive is almost always used, as this class of adhesive is considerably more resistant to aging, even at elevated temperatures. The shear load capacity is also higher.
1.1.4 Insulation class H (180°C) and C (205°C)
For class H, thermosetting acrylate adhesives can still be used. At higher temperatures, only polysiloxane adhesives are used.
These polysiloxane adhesives are extremely resistant to temperature and aging. They also adhere to surfaces that are anti-adhesive. They are therefore suitable for bonding siliconized or waxed materials. Due to their high internal strength (cohesion), they can be removed without residue even after exposure to temperature and remain permanently elastic for a long time even at high temperatures (no embrittlement).
2 Properties of adhesive tapes
The combination of electro-insulating film and technical adhesive results in adhesive tapes to which certain expectations are attached. Some of the properties of the film and adhesive have already been mentioned.
However, further information, especially on mechanical properties, is of interest:
2.1 Tensile strength/tear force
Tapes used for bundling and wrapping in particular require a high tensile strength. This tensile strength is usually specified in N/10mm (tensile force). Glass fabric can reach some 100N. The tensile strength according to IEC 60454-2 indicates when the tape actually breaks.
2.2 Elongation at break
It indicates at what percentage elongation an adhesive tape tears. For polyester with 25µ thickness, this is around 80-120%.
2.3 Burning behavior
Specifies how long a test strip of the adhesive tape continues to burn according to a standardized procedure. The aim is, of course, to keep the burn time as short as possible. This is best achieved by Kapton® or Nomex®.
A test method is described, for example, in IEC 60454 or in the American standard UL510. The definitions describe products that are flame retardant or flammable.
2.4 Electrolytic corrosion effect
The corrosive effect of certain adhesive tapes in long-term use should not be underestimated. This effect is measured on a cleaned and pickled brass surface.
The best value for the corrosive effect according to IEC 60454 is A 1. Values better than AN 1.4 are considered non-corrosive.
2.5 Rolling force
Particularly in the case of automated taping of coils or wraps, the force required for unwinding is of interest (i.e. the force with which the tape adheres to its back is meant). If this force is too high, the tape will stretch slightly and may creep back later. This can lead to holes in the insulation or the so-called "flagging" (the end of the tape detaches from the spool and forms a "flag").
2.6 Shear strength
The shear strength is tested by applying a vertical weight (e.g. 1 kg) to a defined adhesive surface (e.g. 625 mm²) and waiting to see whether and after what time the tape shears off. This tests the internal cohesion of the adhesive. Since most electrical insulating tapes are used at elevated temperatures, the test can also be performed in a heating cabinet. Some CMC Klebetechnik adhesive tapes resist shearing even at 220°C.
2.7 Dielectric strength
Of course, it is particularly interesting for the use of an insulating foil to know up to which voltage it can be used. The dielectric strength indicates at which voltage a breakdown actually occurs. The measurement is usually made by a voltage ramp of 500V/sec until a predetermined current flow is reached, which is then defined as "failure of the insulation".
2.8 Adhesive strength
This information in the data sheet is one of the most important for many users. This is because it states the quality of the adhesive tape in relation to its purpose. Often, the highest possible adhesive strength is required, but in many cases this is not absolutely necessary.
The adhesive strength is measured by applying a 10 mm (25 mm) wide adhesive strip to a cleaned stainless steel plate (2x pressing with a 2 kg rubber roller). The adhesive tape is then folded over by 180°. The peel force is then measured at 300mm/min.
When interpreting the data sheet information, it is also important to know when this peel force is measured. With almost all adhesives, the adhesive force increases significantly over time (approx. 24 hours), quite possibly to twice the world obtained by immediate peeling.
In addition to this information, there may be further characteristic data required in individual cases. The best results in practice are achieved when experts from the user and CMC Klebetechnik work together in good time.
2.9 Creepage distance formation
If an insulation foil is permanently operated at voltages above approx. 600V, the corona discharge (discharge into the air) can cause damage to the insulation. This damage increases sharply as the voltage rises. In the process, carbonaceous deposits are formed due to the degradation of the material, which leads to a conductive coating. This leads to loss of the insulation effect.
In order to be able to quickly determine this degradation of the insulation properties, a conductive liquid is dripped between two platinum electrodes with increasing voltage in accordance with IEC 60587. The result of the test procedure is a certain value of the resistance to creepage path formation.
Since there are other standards for determination, the specifications differ: For example, a good value for an insulation material is (unitless) "1" or insulation class I or the specification of the passed test voltage 450-599V. Polyester films have this good value, while unfilled Kapton® HN films have the relatively low value of 4 (IIIB, 100-174V). A good measure against this path formation is to prevent corona discharge. This is most easily achieved either by sufficient spacing (field strength) or by impregnating and potting, as this avoids the discharge paths through the air.
In addition, of course, dirt and humidity also have a significant influence on the formation of creepage paths.
2.10 Chemical compatibility, insulation systems
Insulation tapes are always used in conjunction with many other products such as enameled wire, impregnating resins and other insulation materials. Therefore, it is necessary that these individual products do not negatively influence each other. The usual, principle approach is to define an insulation system.
Insulation systems (e.g. DIN EN 61857) are the summaries of various insulation materials used in a device (e.g. electric motor). In principle, the chemical compatibility of the individual components is tested under elevated temperatures. After a specified time, the insulating capacity of the insulating varnish on the copper wires must still withstand certain minimum requirements. Such tested systems further increase the safety of a development, since chemical reactions that damage the insulation system are not to be expected.
Talk to us if you are planning to use a tape. Our specialists can best support you in your project if they are involved at an early stage.
Basics of bonding and adhesive properties