In many cases, the offer goes beyond pure PCB assembly to electronics development, material management and (final) assembly of entire modules. This is when CMC Klebetechnik products (films, die-cutted parts, coatings) come into play. This is because the insulation of circuit boards, transformers, power capacitors or transistors is an elementary component of every electronic or mechatronic assembly. Insulation films must be selected individually depending on the place of use and the general conditions such as temperature, vibration, mechanical load, voltage levels and frequency.
CMC Klebetechnik offers extensive expertise in technical films and coatings. They can help to make electronic assemblies more compact, more reliable and more durable. They can also make assembly considerably cheaper (die-cutted parts made from insulating films) or simplify assembly production because creepage distances are created differently and air gaps are reduced - from prototypes to PCBs ready for series production.
Application technology
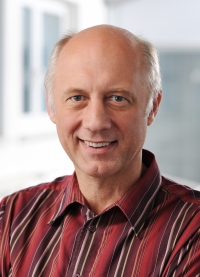
If you have any questions, please contact:
Gerald Friederici
Phone: +49 6233 872 356
E-Mail:
friederici (at) cmc.de
The example of a Kapton® film clarifies the above statement:
If you want to build a particularly compact electrical/electronic device, you come up against various limits. The smaller the device, the higher the energy density. In the simplest case, this means a higher temperature load. Within certain limits, components with a corresponding temperature class can be selected.
For insulation films, this means, for example: If the temperature load regularly or permanently exceeds the limit of 130°C, the very good and inexpensive polyester film can no longer be used as insulation film. Its upper limit is 130°C (class B) and its service life at this operating temperature is just 2.5 years. At this point, the dielectric strength has dropped by 50% due to ageing alone. Adhesive tapes made from Kapton® films, on the other hand, are designed for up to 180°C and have a very long service life.
However, a compact design is not only achieved by increasing the energy density and using higher temperature-resistant components. This is an "expensive" process. It is better to dissipate the heat effectively so that the temperature does not rise in the first place. In electronics production , this is achieved primarily by thermally conductive products such as thermal pads, thermal paste or very thin, thermally conductive insulation foils made of Kapton® MT.
Polyester films would be counterproductive in this case, as they have a much higher thermal resistance and therefore tend to hinder heat dissipation.
EMS service providers naturally know of other ways to increase the structural density. However, the standardized clearance and creepage distances must be observed. These become smaller (more compact) the cleaner the environment is (pollution class) and the higher the temperature class is. Above all, however, the sensitivity to creepage path formation must be low (cti value, comparative tracking index). Polyester film has a clear advantage in this respect (cti=1 instead of cti=4 for Kapton®) and allows shorter tracking paths.
Conclusion: not every plastic film is equally suitable for every electrotechnical application.
Especially when using conventional components (THT), insulation stampings between the component and multilayer boards (PCB, FPC, RPC) can make a contribution. They help to save space and still ensure reliable insulation. In addition to the electrical function, heat loss can also be dissipated by equipping the insulation die-cut parts with heat conductors.
EMS producers have experience in the conception, design and production of printed circuit boards, electronic components and devices for their customers. CMC Klebetechnik, on the other hand, offers extensive expertise in technical films and coatings. They can help to make electronic assemblies more compact, reliable and durable. They can also make assembly considerably cheaper (die cutted parts made of insulating films) or simplify assembly production because creepage distances are created differently and air gaps are reduced - from prototypes to PCBs ready for series production.
Of course, the above also applies to companies that carry out other work on a contract basis (contract manufacturing). For example, switch cabinet construction for process technology, conveyor technology, turbine technology, the chemical industry or mechanical engineering, where die-cutted parts made of rigid, stable polyester or polycarbonate film ensure reliable insulation between 19" rack inserts.
There is an almost unlimited number of applications for adhesive tapes in industrial electronics, drive technology, pump control, medical technology, aviation, security technology and white goods, communication electronics and electrical engineering in general - ask us if you feel that a film (adhesive tape, die-cut part) could be the solution for your task. For insulation, fastening, heat dissipation or electromagnetic shielding.
Examples of products that EMS service providers can use in electronic assemblies, for example:
CMC 278xx is a range of polypropylene films with very special properties. The material is classified as flame-retardant in accordance with UL94 V0 and has a very good comparative tracking index of cti=0. The material is excellent for die-cutting and bending. This means that sheet steel housings, for example, which are used as flame barriers, can be replaced by a significantly lighter solution. Thanks to its very good insulating properties, the self-adhesive PP material can also be used as insulation under large components on PCBs (printed circuit boards).
CMC 70100 or CMC 70105 are Kapton® adhesive tapeswhich are designed for class H (180°C continuous temperature). They are used in transformers, transformers and coils as basic insulation, interlayer insulation or terminating bandages
Thermally conductive silicone films such as CMC 15005 are used to thermally connect high-performance electronic components to heat sinks (heat sinks). Softer silicone films and gap fillers can also ensure a thermal connection to heat sinks under power capacitors or supercaps. Fan controllers for air conditioning systems, motor controls for actuators, controls for modern electric stoves or power LED assemblies also benefit from a good thermal connection.
die-cutted parts from Polyester film, PEN film or Nomex® and Kapton® (polyimide) fulfill a variety of insulation tasks in electronic assemblies or mechatronic solutions.
Die-cutted parts made of metal films, which can also be (partially) insulated, are used as EMC protection in many housings and between circuit boards. Even a thin film attenuates electromagnetic interference very well. Products such as CMC 91743 or CMC 91815 are also used for EMC shielding. These copper film adhesive tapes have an electrically conductive adhesive that can be used to conduct shielding currents to earth.
Particularly thick polyester films, e.g. CMC 29250 (250µm thick PET film; UL-listed) have sufficient inherent rigidity, e.g. to form sufficient insulation between electronic plug-in units in switch cabinets in order to be able to build more compactly (keyword: clearance and creepage distances)
Double-sided adhesive tapes such as CMC 10718 or linerless transfer adhesive tapes such as CMC 15581 replace joining methods such as screwing, welding or clamping. Such adhesive tapes bond different surfaces (e.g. circuit board and housing) flat and stress-free. They are easy to install and compensate for differences in thermal expansion (e.g. plastic to steel) much better than point fixings with screws, for example.
If there is a risk of partial discharge in high-voltage applications (e.g. medical technology), particularly resistant adhesive tapes such as CMC 70300 (Kapton® CR) can help to increase the service life of the product.
CMC Klebetechnik offers suitable, thermotransfer printable label materials with high heat resistance for marking circuit boards even before the wave soldering bath (reflow), for example.
Adhesive tapes from 0.8 mm width are used to increase clearance and creepage distances
In general, electrotechnical adhesive tapes (e.g. CMC 10966, PET or CMC 70110, PI) are often used for fixing and fastening e.g. connecting wires in electronic assemblies.
Insulated copper films (CMC 38xxx product series) are used as flat conductors for high frequencies or high currents - or as shield windings in transformers. The insulation can be single, but also double and triple with copper widths of up to 150 mm. This means that large cables can be transported in a space-saving (flat) manner.
During development and rapid prototyping (E²MS), adhesive tapes and punched parts from CMC Klebetechnik can also be supplied in very small quantities in order to carry out feasibility studies. In particular, the two high-precision and very large cutting plotters from ZÜND enable small series from a quantity of 1.
Insulating films, adhesive tapes and die-cut parts for EMS manufacturers